흔히들 이어폰 분배기나 허브라고 부르는 물건을 만들기도 했다. 최근에 3D 모델링을 부족하게나마 독학했으니 배운 걸 써먹어 볼 겸 3D프린터로 케이스를 뽑아 깔끔하게 만들어보기로 했다.
이어폰 단자 Male 한 개, Female 두 개를 핀 맞춰서 연결만 잘 해 주면 되는 굉장히 단순한 구조다. 외형을 그럴싸하게 만드는 게 중요하다는 말이다. 이어폰 단자는 안 쓰는 핸드폰과 이어폰들에서 뜯어서 조달했다.

그리하여 탄생한 인생 첫 3D 모델링이다. 케이스 만들어서 드릴로 구멍 뚫고 부품 넣어 연결하고 뚜껑 닫으면 되겠지라고 안일한 생각을 했다. 망하면서 배우는 법이다.
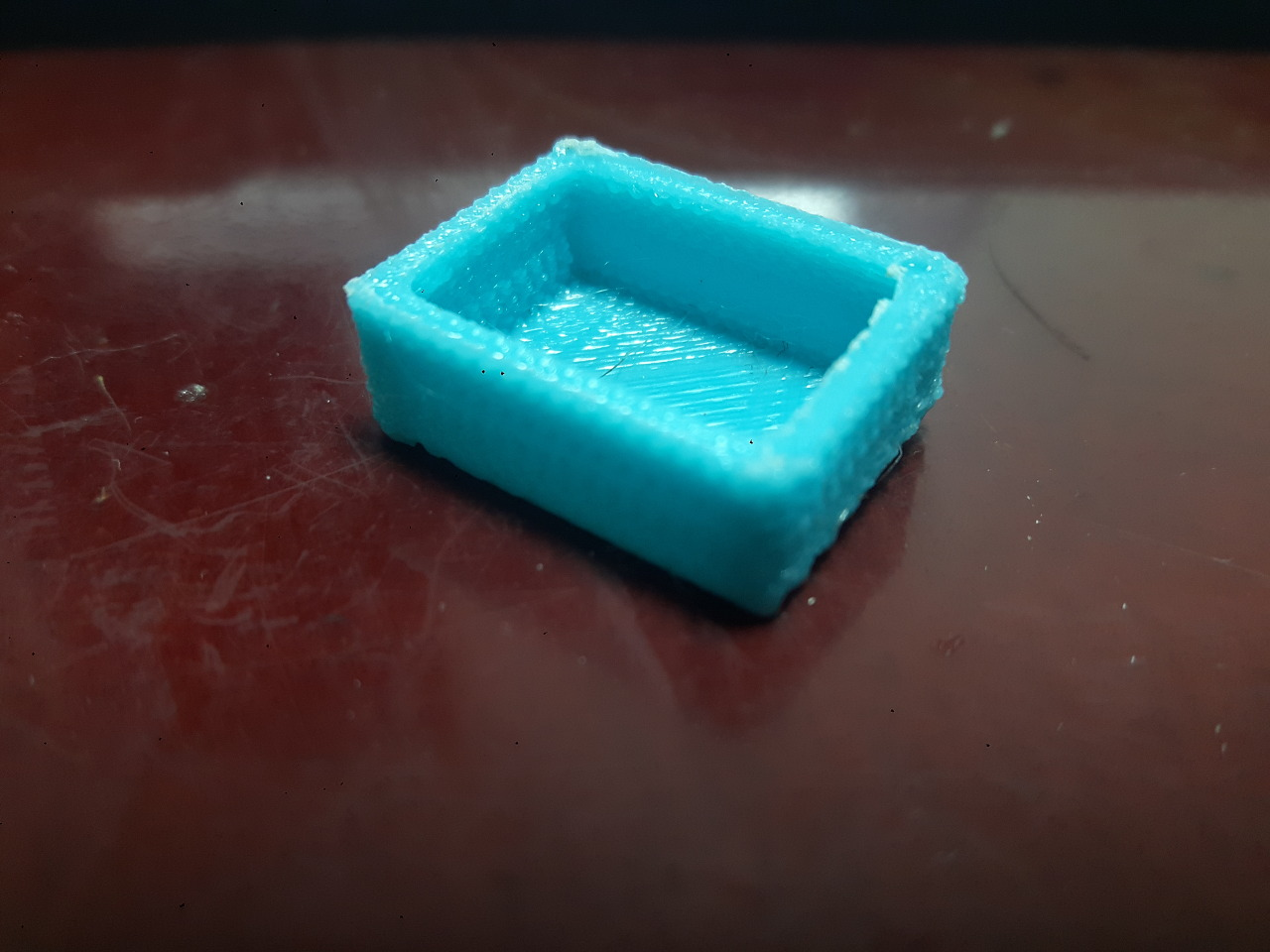
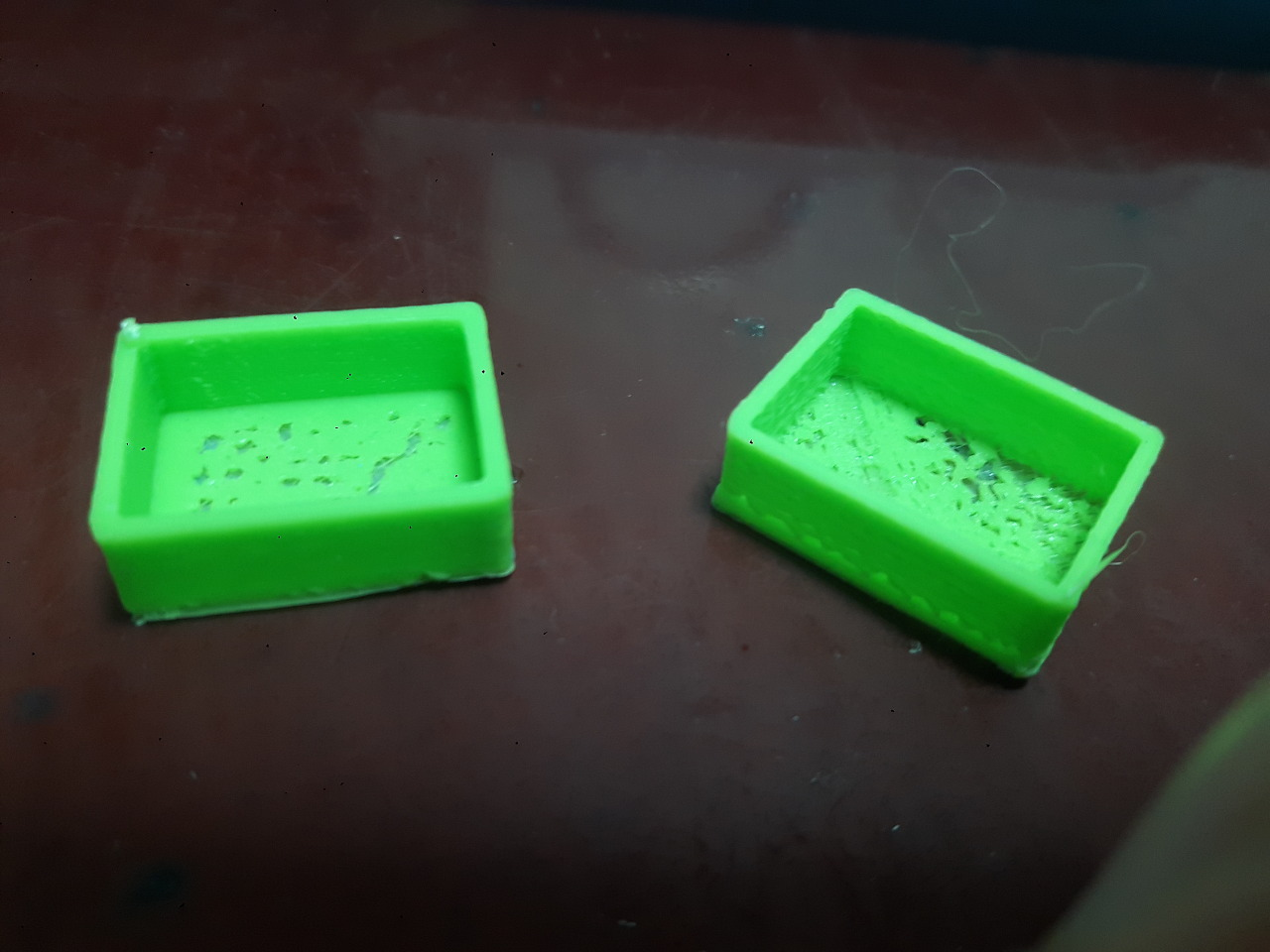
망했다. 이걸로 3D 모델링이 그냥 물건을 예쁘게 뽑아내는 게 아니라는 걸 알게 됐다. 3D 모델링은 기계가 어디까지 해낼 수 있는지를 상상 속의 모델링과 저울질하는 현실과의 타협이다. 3D 프린터의 특성을 전혀 고려하지 않았다.
3D프린터의 노즐 직경은 0.4mm인데, 외벽 두께를 아무 생각 없이 1mm로 설정했다. 결과적으로 노즐이 두 번 움직여 0.8mm를 쌓은 후, 나머지 0.2mm를 쌓기 위해 지그재그로 드드드드 하고 움직이며 출력물을 망쳐 버렸다. 외벽이 빨래판도 아니고 우둘투둘하다. 그래서 외벽 두께를 0.4mm의 배수인 1.2mm로 수정했다.
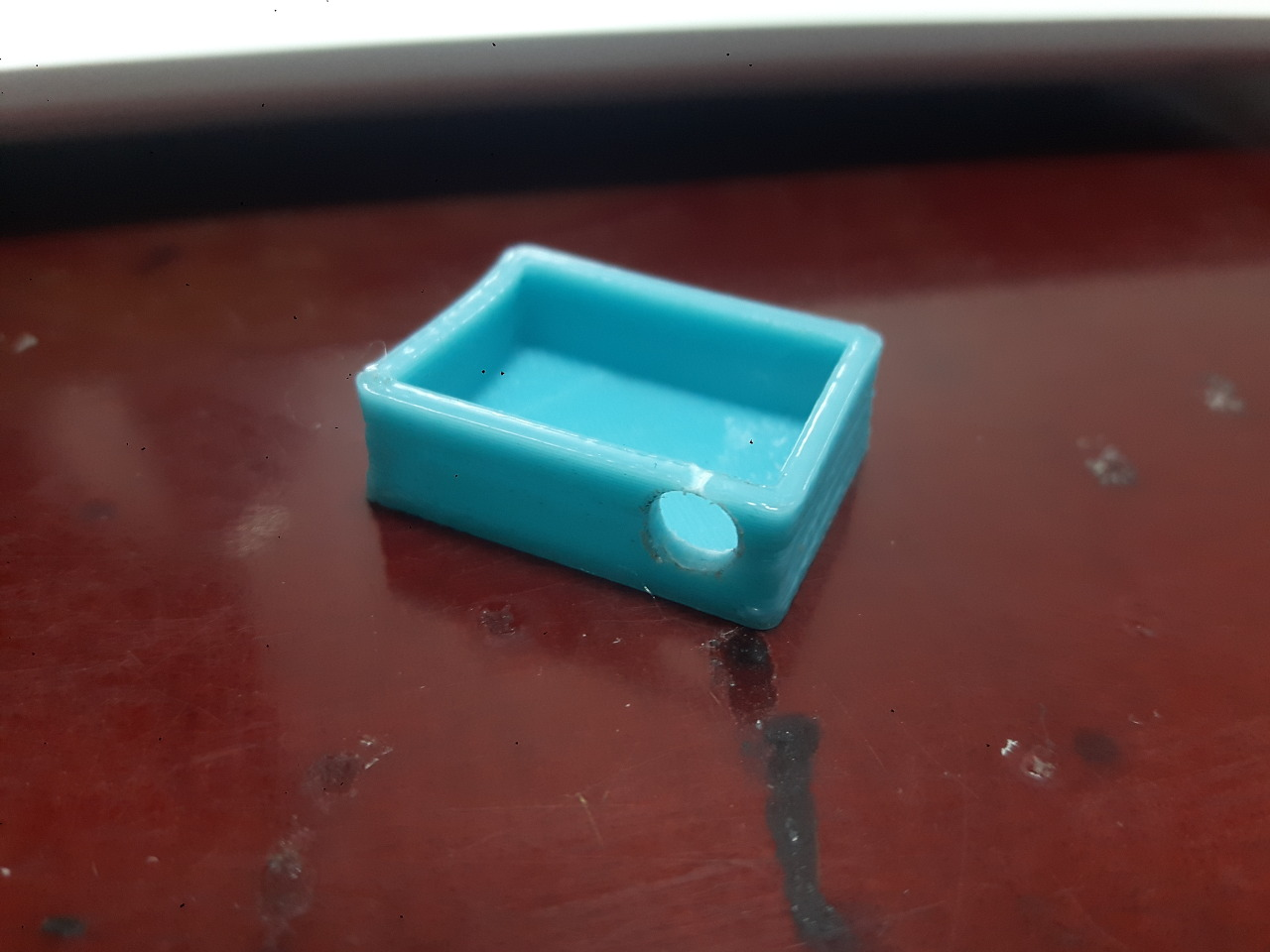
출력물의 퀄리티는 훨씬 나아졌다. 하지만 생각치도 못한 곳에서 문제가 생겼다. 드릴로 구멍을 뚫으면 뿅 하고 예쁘게 뚫릴 줄 알았건만 윗부분이 거의 부러지다시피 했다. 뚜껑을 덮는 방식 또한 출력물이 얇으니 똑바르게 출력되지 않아 포기하기로 했다.

그래서 한 번 더 수정을 거쳤다. 외벽 두께는 당연히 1.2mm로 설정했고, 얇게 뽑으면 생기는 문제 때문에 정확히 반으로 나누어 두 개를 뽑아 합치기로 했다. 반만 출력하니 구멍에 서포트를 세울 필요도 없다.
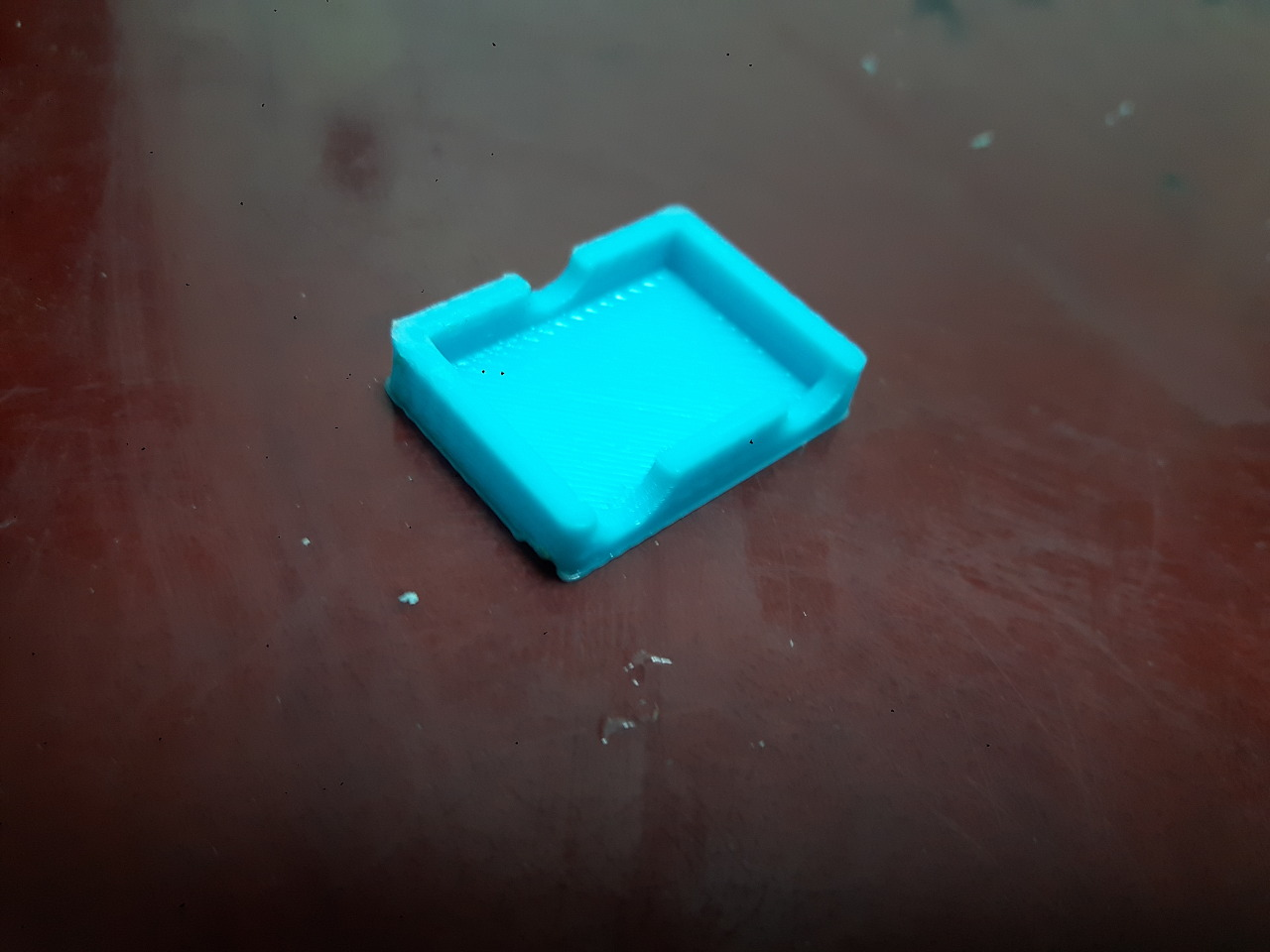
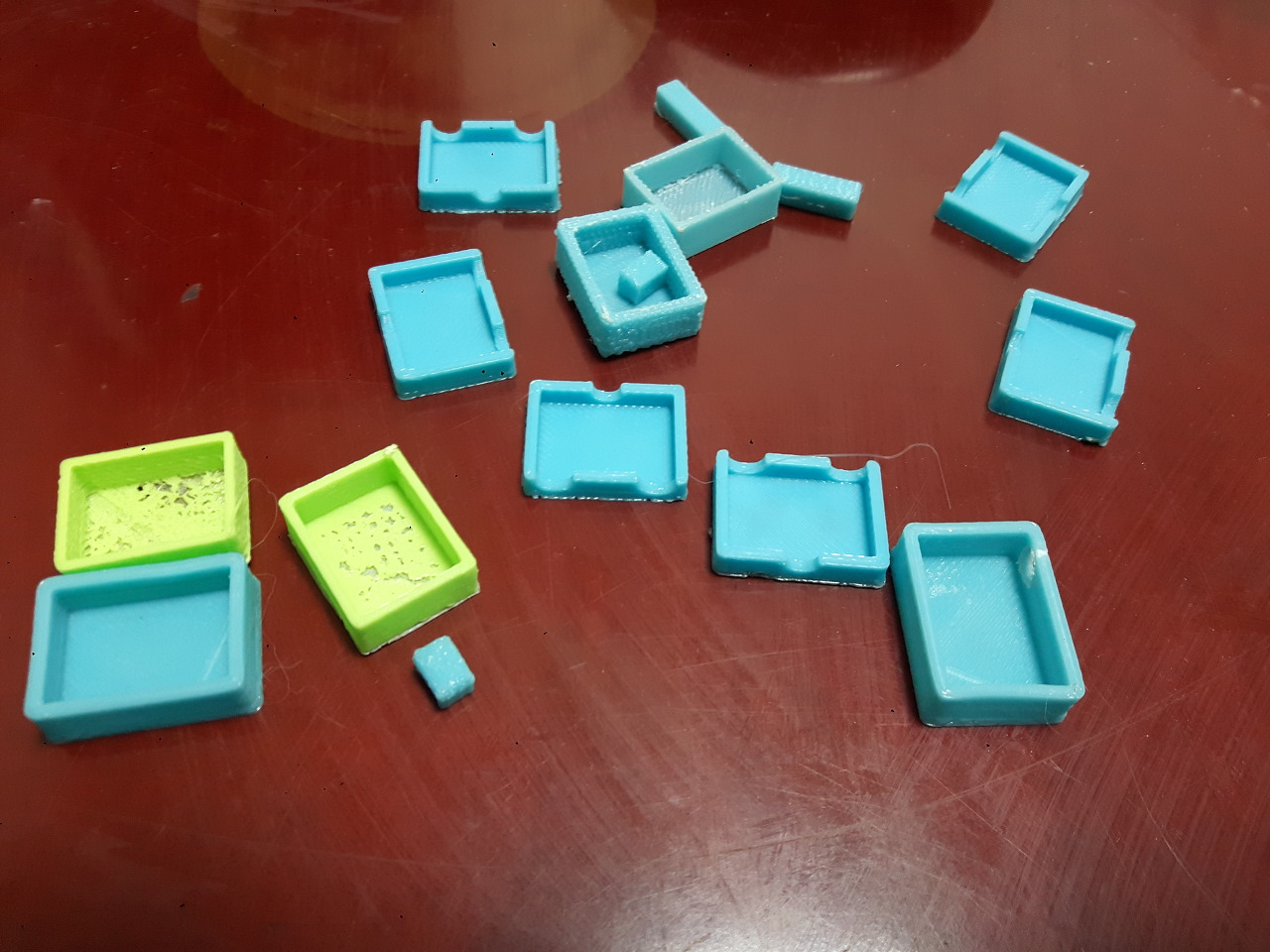
왼쪽이 이 모델링으로 출력한 출력물이다. 오른쪽 사진은 이걸 뽑기 위해 시도한 시행착오들이다. 3D프린터가 어떻게 쓰는 물건인지 슬슬 감이 오기 시작했다.

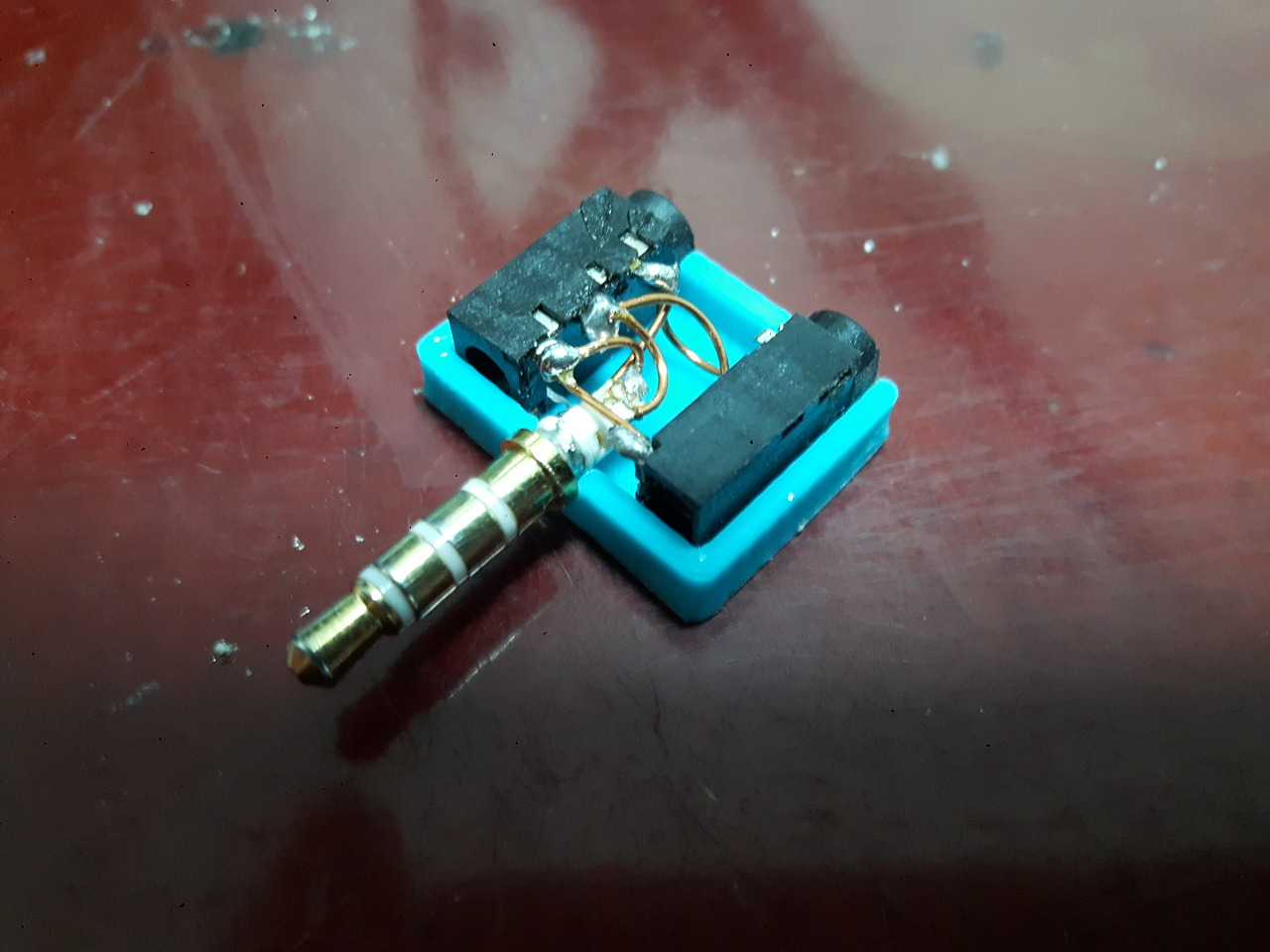

이제 케이스가 준비되었으니 부품을 배치한다. 공간이 좁아 납땜이 쉽지 않았다. 어쨌거나 배선을 마치고 순간접착제를 이용해 부품을 고정시킨 다음, 뚜껑을 닫았다. 출력물 마감이 깔끔하지 않아 사포로 조금 갈아 주었다.
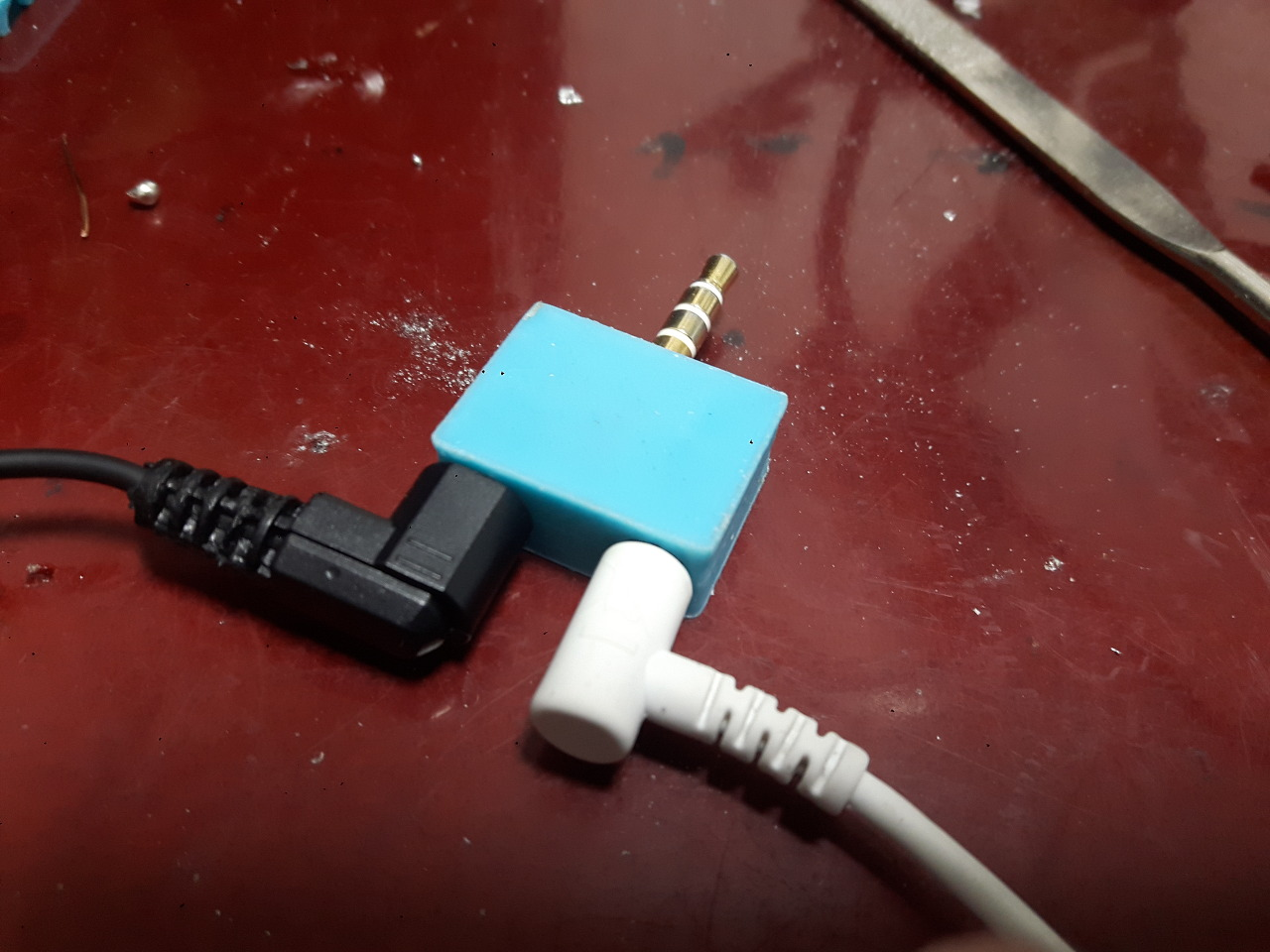
완성한 모습이다. 양 쪽 모두 문제없이 출력이 잘 나온다.